CO2-Reduction | 1st step: Energy saving
Improving energy efficiency and increasing the use of waste heat holds a huge potential for CO2 reduction in industrial processes!
What is the actual status?
In many production processes, HEAT is needed first to make the product. Then COLD is needed to bring the product to storage- or shipping temperature.
Steam is used for heating and cooling water for cooling.
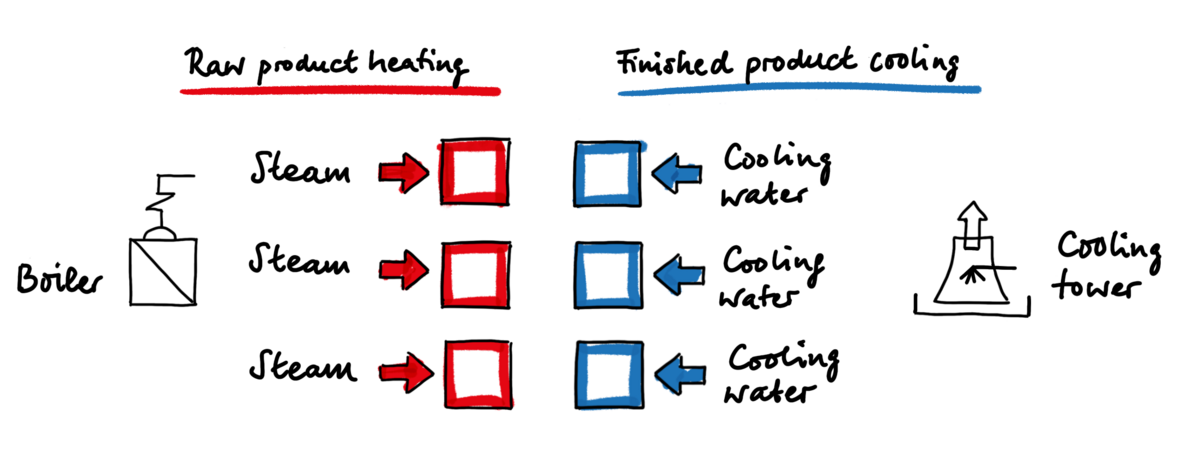
How can we optimise this process?
- Using the waste heat from cooling the finished product to heat the raw products.
- Raising the temperature of the waste heat by installing a heat pump.
- Compensating for different starting points of production processes by collecting of waste heat flows and the use of buffer storage.
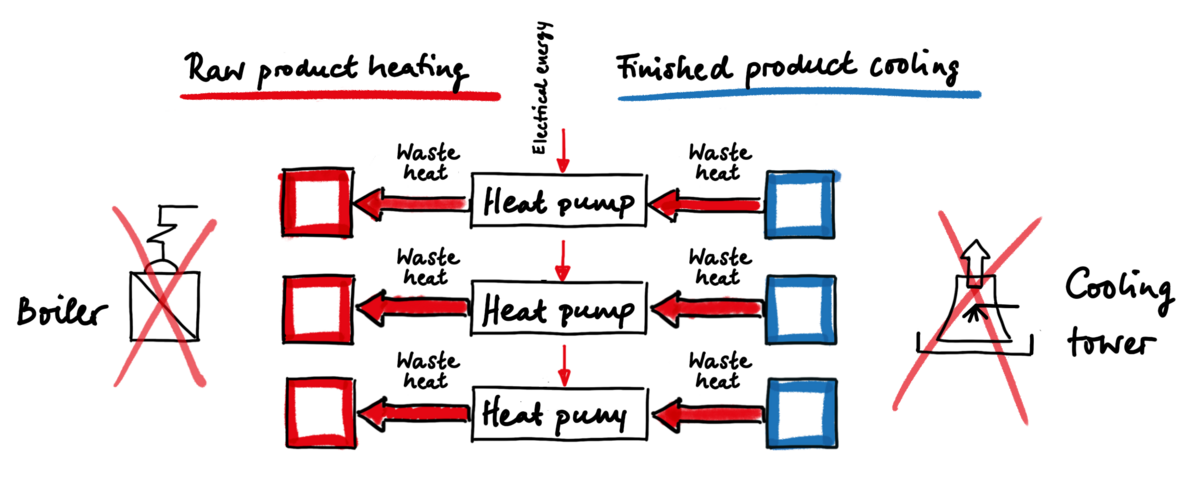
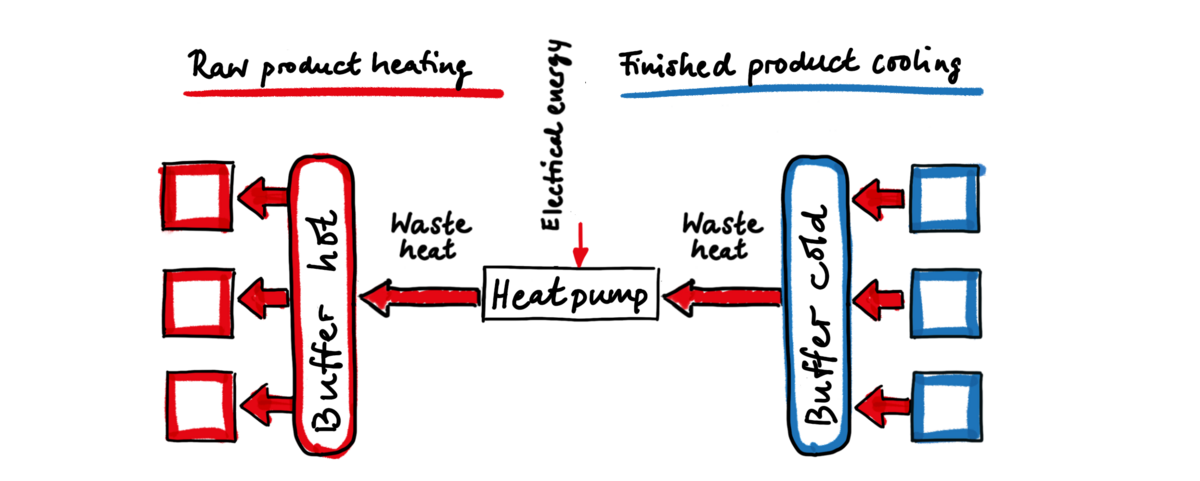
What can we do for you?
- Analysing the effeciency of existing heating and cooling distribution networks.
- Analysing the electricity demand of large pumps and fans.
- Recording of heat and cold consumers in production.
- Recording of time dependencies.
- Development of concepts for optimised waste heat utilisation.
- Design of components, determination of savings, determination of investment costs.
- Detailed planning of your waste heat project.
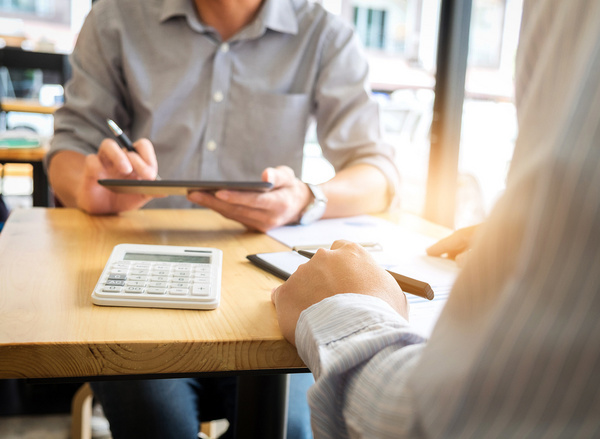
Technologies
Direct heat exchange between heat and cold consumers
Raising the temperature level of the waste heat by heat pumps or vapour recompression
Usage of efficient drives for pumps, compressors and agitators
Mechanical instead of thermal dewatering, dehumidification, drying
Increasing the number of stages in the evaporation process
Switching to vacuum evaporation in evaporation processes
Using vapour recompression for evaporation
Usage of exhaust gas heat exchangers in ovens, dryers and roasters
Installation of hot and cold buffer tanks to compensate different starting points of production steps
Upgrade to mixers with high shear forces in order to switch from "warm mixing" to "cold mixing"
Converting the hall heating to waste heat
Converting the heating of the product water to waste heat